How to Find the Best Packaging Machine Repair Company Near You
How to Find the Best Packaging Machine Repair Company Near You
Blog Article
Quick and Reliable Packaging Equipment Repair Provider to Lessen Downtime
In the competitive landscape of manufacturing, the performance of product packaging operations hinges on the dependability of equipment. Quick and trustworthy repair services are crucial in mitigating downtime, which can lead to significant economic losses and operational problems.
Importance of Timely Repairs
Timely repair work of packaging devices are important for keeping functional performance and decreasing downtime. In the busy setting of manufacturing and product packaging, also small malfunctions can cause considerable delays and productivity losses. Dealing with concerns without delay makes certain that equipments run at their ideal capacity, consequently guarding the circulation of procedures.
In addition, normal and prompt maintenance can prevent the escalation of small issues into significant breakdowns, which typically incur higher fixing expenses and longer downtimes. A proactive method to device repair not just protects the integrity of the tools however also boosts the general reliability of the assembly line.
Furthermore, timely repair services add to the long life of packaging equipment. Makers that are serviced quickly are much less likely to experience too much wear and tear, permitting companies to optimize their investments. This is specifically crucial in industries where high-speed product packaging is important, as the demand for consistent efficiency is critical.
Advantages of Reliable Service Providers
Trustworthy company play a pivotal duty in making sure the smooth operation of packaging equipments. Their competence not just improves the efficiency of repair services but likewise contributes considerably to the longevity of devices. Trusted service suppliers are outfitted with the technical understanding and experience essential to diagnose problems precisely and apply effective services swiftly. This reduces the risk of repeating issues and makes certain that machines operate at ideal efficiency levels.
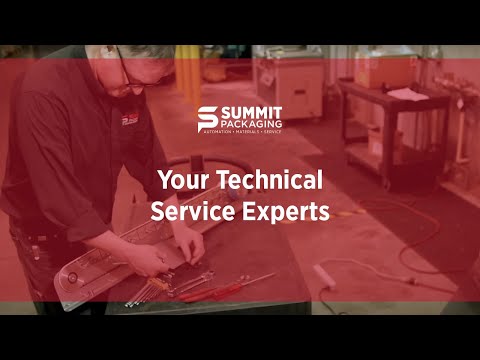
Additionally, a reliable company offers extensive assistance, including training and guidance for personnel on device procedure and upkeep finest methods. This not just encourages workers yet likewise grows a society of safety and effectiveness within the company. On the whole, the benefits of involving trustworthy service suppliers extend past immediate repair services, favorably impacting the entire operational process of product packaging processes.
Usual Product Packaging Machine Issues
In the realm of packaging procedures, different concerns can compromise the efficiency and functionality of devices (packaging machine repair). Another typical problem is imbalance, which can cause jams and uneven packaging, influencing product top quality and throughput.
Electric issues can additionally disrupt packaging operations. Damaged electrical wiring or malfunctioning sensing units may result in irregular device habits, creating delays and raised functional Get More Info prices. Additionally, software glitches can hinder the machine's programs, bring about operational inefficiencies.
Inconsistent item flow is an additional crucial issue. This can develop from variants in item dimension, shape, or weight, which may impact the device's capability to take care of products properly. Not enough training of operators can worsen these issues, as untrained personnel might not identify early indications of breakdown or may misuse the devices.
Attending to these common packaging maker concerns promptly is crucial to maintaining performance and making certain a smooth procedure. Regular examinations and positive maintenance can significantly reduce these worries, cultivating browse around this web-site a reliable packaging environment.
Tips for Reducing Downtime
To reduce downtime in packaging procedures, applying a positive upkeep technique is essential. Routinely scheduled maintenance checks can recognize prospective issues before they intensify, making sure equipments run successfully. Establishing a routine that includes lubrication, calibration, and inspection of critical parts can dramatically minimize the frequency of unanticipated breakdowns.
Educating staff to operate equipment appropriately and identify very early warning signs of breakdown can additionally play a vital role. Encouraging drivers with the knowledge to execute fundamental troubleshooting can avoid minor concerns from causing significant delays. Furthermore, preserving an efficient stock of crucial spare parts can expedite repairs, as waiting for parts can result in extended downtime.
Furthermore, recording maker performance and maintenance activities can aid recognize patterns and frequent troubles, enabling targeted interventions. Integrating sophisticated surveillance modern technologies can provide real-time data, making it possible for anticipating upkeep and reducing the risk of sudden failings.
Lastly, fostering open interaction in between drivers and maintenance teams makes sure that any irregularities are promptly reported and resolved. By taking these positive actions, organizations can enhance functional efficiency and dramatically minimize downtime in product packaging procedures.
Selecting the Right Repair Solution
Choosing the proper fixing solution for packaging machines is a critical choice that can considerably affect functional performance. A well-chosen service copyright makes sure that your equipment is repaired promptly, properly, and to the highest criteria. Begin by evaluating the copyright's experience with your specific type of product packaging tools. A technician knowledgeable about your equipment can identify concerns a lot more accurately and execute solutions much more rapidly.
Following, consider the company's online reputation. Looking for comments from various other companies within your sector can give insights right into integrity and high quality. Accreditations and partnerships with identified equipment producers can also show a dedication to quality.
Furthermore, examine their action time and accessibility. A company who can provide prompt support minimizes downtime and maintains production flow constant. It's additionally critical to inquire about service warranty and solution warranties, which can reflect the self-confidence the company has in their work.
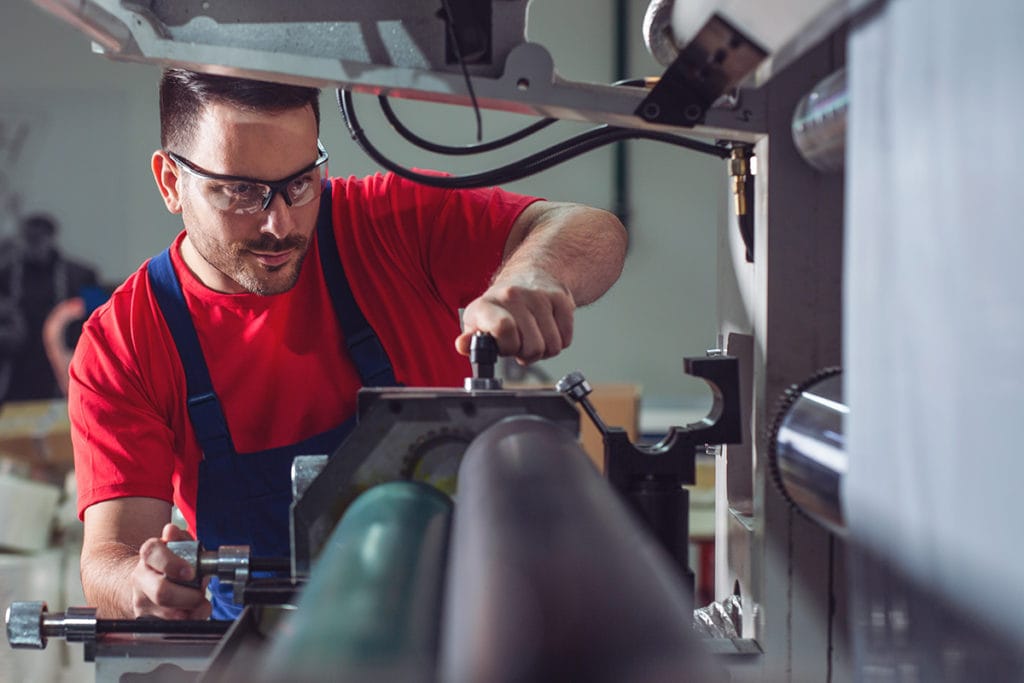
Verdict
To conclude, the relevance of quick and reliable product packaging device fixing services can not be overstated, as they play a critical duty in decreasing downtime and making sure operational efficiency. By prioritizing timely repairs and picking trustworthy company, organizations can effectively keep and resolve common issues productivity. Carrying out positive maintenance methods and purchasing staff training further improves the longevity of packaging equipment. Eventually, a critical strategy to repair solutions fosters a more durable production atmosphere.
Timely fixings of packaging makers click for source are important for preserving functional efficiency and lessening downtime.Additionally, timely repair services contribute to the long life of packaging equipment. On the whole, the advantages of engaging trusted service suppliers expand beyond immediate repair services, favorably affecting the whole operational process of product packaging processes.
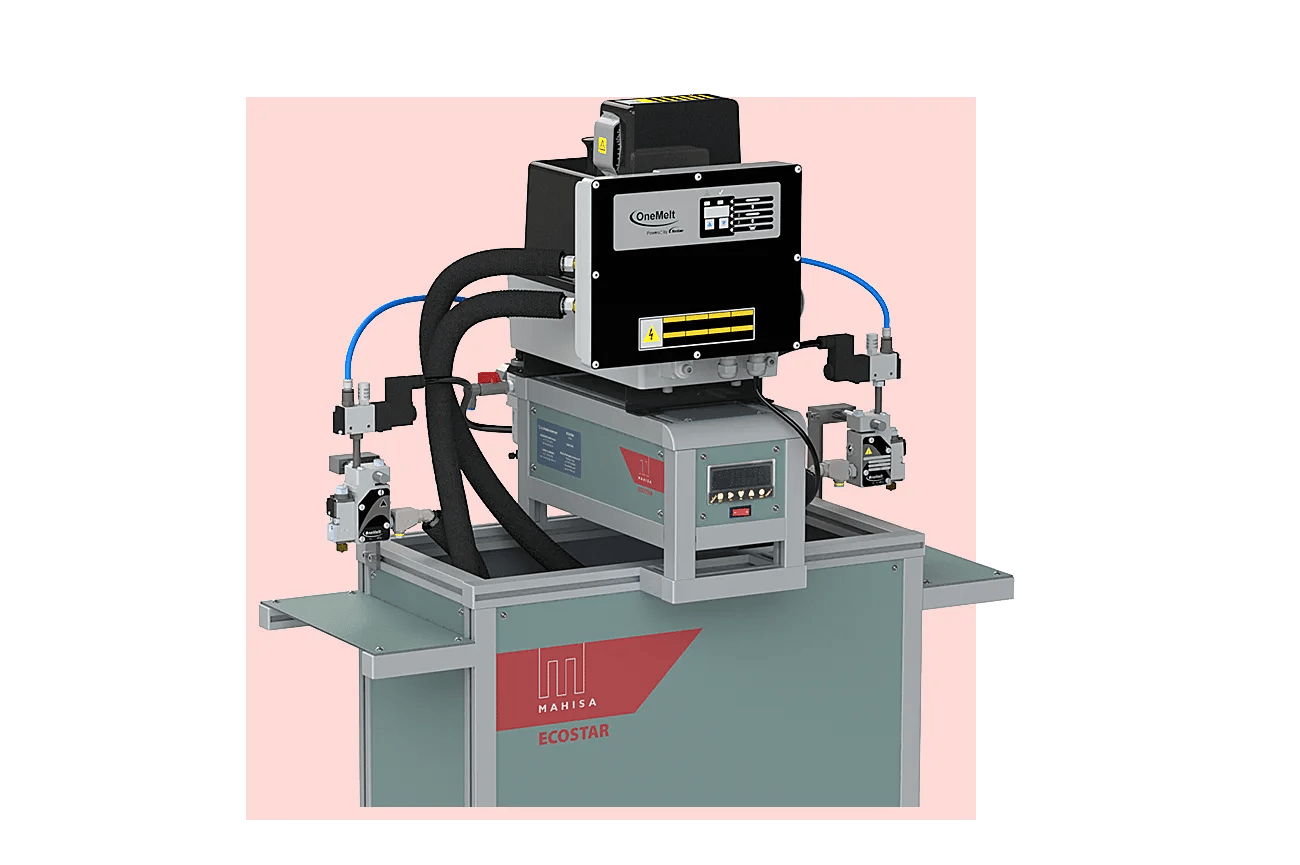
Report this page